Research project combines digitization and process engineering
Digital Fire: Biomass combustion digitized
In the »DigitalFire« project, the Fraunhofer Institute UMSICHT is exploring the possibilities of digitizing biomass furnaces. Cost-effective standard components should make existing plants more flexible and economical. The project has a duration of three years and is funded by the Federal Ministry of Food and Agriculture with approximately 776,000 EUR.
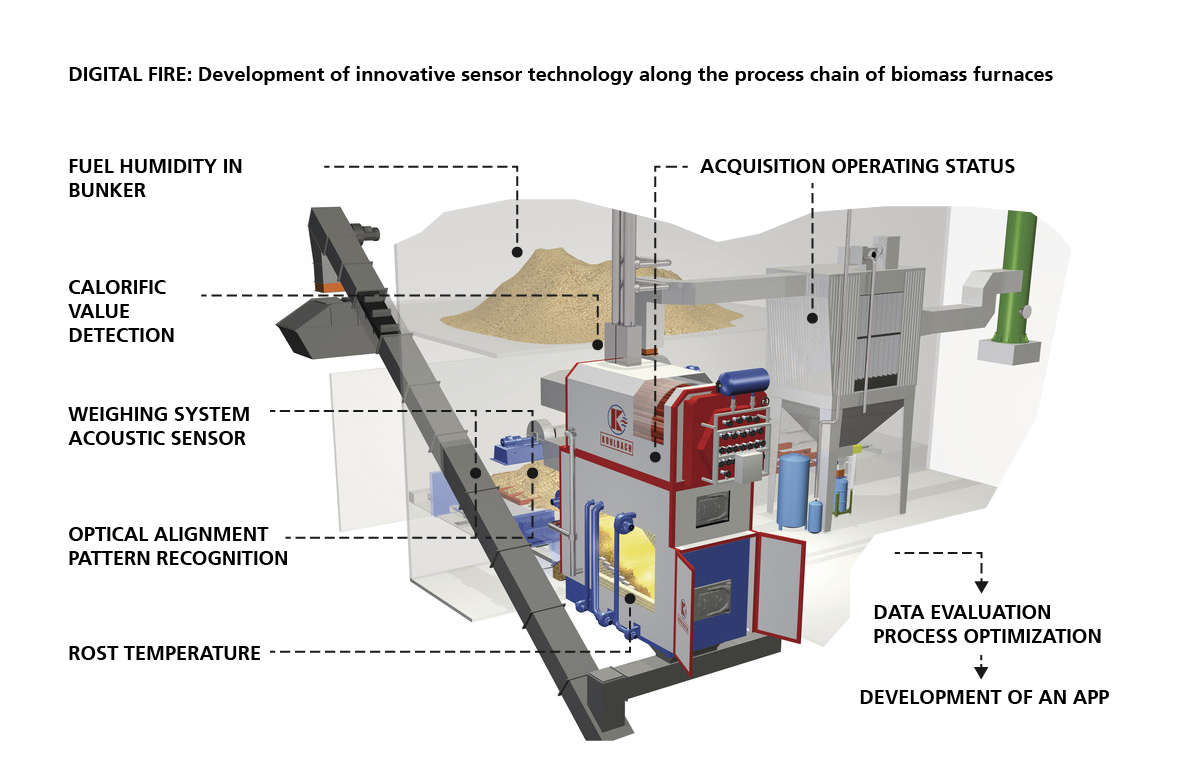
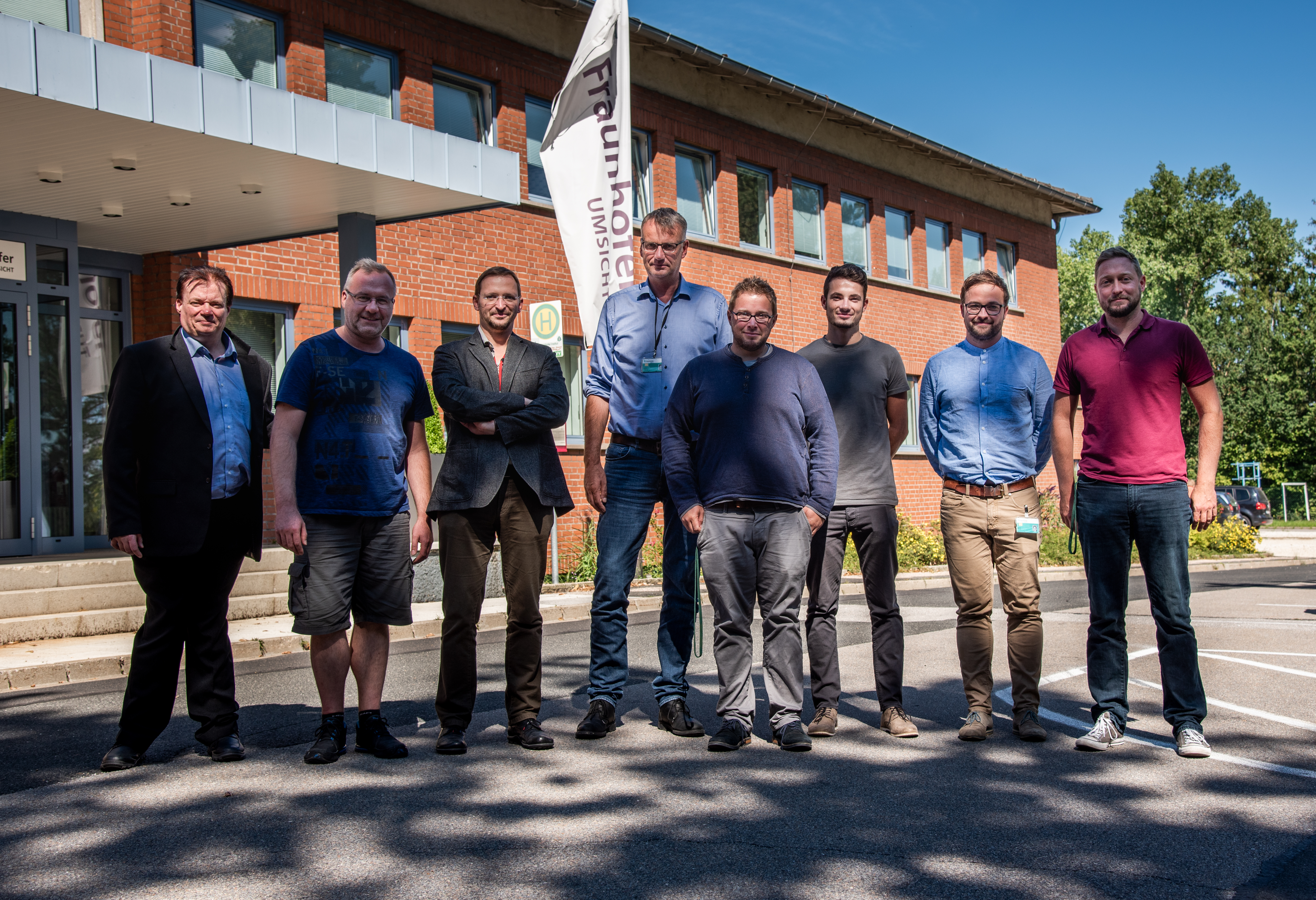
Digitisation and biomass firing: »Can't we? It's possible«, say researchers from the Fraunhofer Institute for Environmental, Safety and Energy Technology (UMSICHT). »DigitalFire will exploit the digitalisation of biomass combustion plants. We will develop modules along the entire process chain and test them in real operation to generate a wealth of additional data. These can then be used to make the systems more efficient and thus more economical, explains project manager Martin Meiller from Fraunhofer UMSICHT in Sulzbach-Rosenberg.
There are approx. 900,000 biomass boiler plants and approx. 700 biomass cogeneration plants in Germany. For economical operation, these plants must increasingly be able to process fuels of lower quality, including biogenic residues. Most systems are basically capable of doing this and also have corresponding programs for input materials such as pellets, wood chips or chips. For fuels such as residual forest wood or biogenic residues, however, the parameters must be set manually. This is complex and requires a lot of experience. Ultimately, the aim is to adjust the combustion control so that a stable combustion process with high burnout quality of solid matter and gas phase and thus a high degree of efficiency is achieved. Mistakes in the setting of the firing system lead to higher emissions and in the worst case to higher wear with maintenance consequences and downtimes. This is where digital technology comes into play: If progress in control and regulation technology makes it possible to achieve lower fuel qualities while maintaining the same performance, an economic benefit is quickly achieved.
To achieve this goal, various sensors, »soft« sensors and data acquisition systems will first be installed in the project. The data generated, e.g. on the calorific value, fuel composition and quality, grate temperature and plant condition (see figure) are collected, processed and visualized. Subsequently, machine learning methods or artificial neural networks are used to evaluate the data and make it usable, e.g. for automated adjustment of the optimum firing parameters or warnings of critical plant conditions. A user-friendly front-end - also for mobile devices (e.g. an app) - should ensure that this information is always directly available to the operator.
Normally, such continuous digital process monitoring of the firing system is only used in large biomass cogeneration plants or waste incineration plants, mainly for cost reasons. In the project, these functions are now also to be made available for furnaces in smaller output classes (boiler plants or smaller biomass power plants from 100 kW up to 20 MW rated thermal output).
To keep the technology affordable, Fraunhofer scientists are taking advantage of falling costs for electrotechnical components, sensors and software solutions. Martin Meiller: »On the one hand, we will look at hardware available on the market, i.e. sensors, measuring components or camera systems. On the other hand, there will also be open source software and AI libraries, for example for optical image recognition. Then we check what we can use for biomass combustion and which modifications we need. All in all, we hope that this will keep the investments for the operators low in order to quickly make a profit«.
The company BFAutomation GmbH & Co. KG is involved as a project partner. It supports the researchers in the development and integration of the new modules. The setup and integration into the server infrastructure, data evaluation and application development will be carried out by IT specialists from the Fraunhofer sites in Oberhausen and Sulzbach-Rosenberg.
The project is financed by the Agency for Renewable Resources (FNR) of the Federal Ministry of Food and Agriculture (BMEL) and has a volume of 814,402 €. The kick-off meeting on 3.9.2019 marked the start of the project, which runs until 2022.
Last modified: